The next generation of cars needs a clearer interconnect strategy
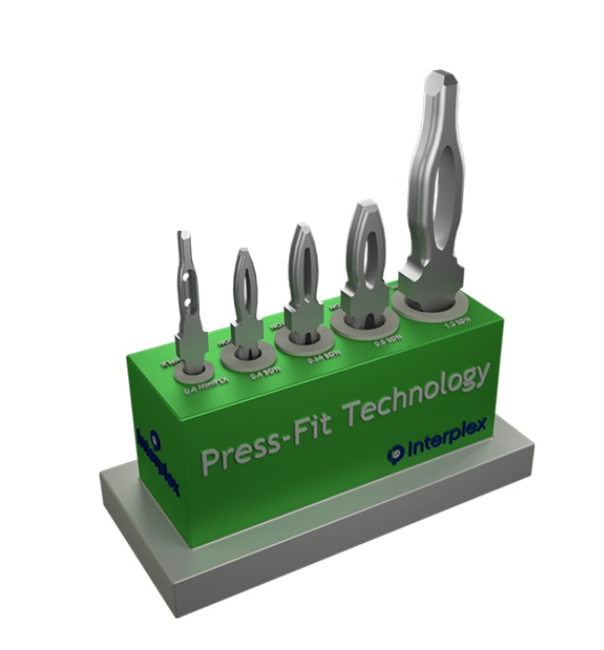
Today's automotive design is becoming increasingly complex, in order to improve comfort, improve performance and ensure higher safety, many vehicles are designed to incorporate more complex features. The number of sensors and imaging devices installed in cars is also increasing dramatically. This is not only happening in the luxury market, mid-range and even economy models are also adding extra features.
At the same time, other dynamics are changing the way car design is implemented. In order to reduce weight and extend the range of electric vehicles (EVs), the mechanical systems used in the past are being phased out and replaced by electronic drive-by-wire systems.
These two different trends will lead to the same inevitable result. The amount of data generated and transmitted by the average vehicle today is orders of magnitude greater than that of conventional cars in the past. In addition, it should be noted that as cars become more autonomous (and we begin to move toward fully driverless vehicles), the amount of data will only get bigger.
The data explosion and its implications
McKinsey, an analytics firm, estimates that the average vehicle now generates around 25GB of data per hour, but that's just the beginning. The number of cameras installed inside and outside the car body continues to increase, and 3D imaging technologies such as Lidar, time-of-flight (ToF) and ultrasound will become a common feature in just a few years.
If automotive systems are to be fully prepared to cope with unprecedented data demands, supportive interconnect solutions need to evolve accordingly. In addition, the way such solutions are built and delivered to the market will also change fundamentally.
Implement interconnect devices in automotive systems
For interconnect devices to function in challenging automotive environments and meet stringent international standards such as LV214 from the European Union and USCAR2 from the American Society of Automotive Engineers, multiple attributes are required. First, they need to be able to withstand shock and vibration, and second, to account for exposure to high temperatures. However, as the auto industry shifts from fuel vehicles to electric vehicles, this problem will gradually diminish.
The presence of electromagnetic interference (EMI) sources, if not addressed, may adversely affect the signal integrity of the transmitted data. In order to solve this problem, it is necessary to add a shielding device in the module. Over time, the appearance of tin whiskers can have a serious impact on the reliability of the interconnect, and there is a possibility of short circuits, which can lead to system failure.
In addition, the space constraints of vehicle design mean that automotive-grade interconnect devices must be extremely compact. This often requires high-density solutions. In some cases, these solutions may require a combination of power and data transmission.
Solve assembly problems
In addition to considering the performance and reliability of the interconnect devices themselves, tier-1 suppliers of electronic control units and sensor modules must also consider the impact of interconnect device integration on the production assembly process. If the installation of interconnects slows down the workflow by increasing the number of necessary steps, this will mean that output will suffer. For example, if the PCB needs to be rotated to change orientation, time will be wasted. In addition, if the assembly of connected devices requires human intervention (as opposed to full automation), the entire process will take longer (and the risk of error will be greatly increased).
In view of the above problems, the crimp interconnection technology is getting more and more attention. Crimp connections provide a reliable and simple connection. By using this technology, assembly work can be significantly more efficient and complex, labor-intensive and chaotic processes such as welding can be avoided.
Solderless connections offer another significant advantage. The solder paste is completely rigid and therefore prone to cracking when subjected to impact or vibration, while the crimped connection has a greater tolerance. As a result, modules with crimped connections have a longer service life than modules with welded pins.
Interplex's crimps connections are now widely used in automotive systems and are recognized by many Tier 1 suppliers. Ranging in thickness from 0.4 mm to 0.8 mm, they provide continuous and reliable operation and are easy to assemble. In addition to mechanical robustness, they have strong retention and industry-leading thermal characteristics.
With its patented IndiCoat electroplating technology for crimped Interplex, Interplex was able to overcome tin whiskers, a challenge for other connector suppliers. Based on this, the quality of the final product can be guaranteed for a long time.
Many automotive companies want to outsource the design of electronic control units or sensor modules, and instead of doing it in-house or with their tier 1 suppliers, many are now relying on Interplex to do this work, thereby focusing engineering resources where they can gain the most differentiation.
The key to Interplex's response to customer projects has been the modular manufacturing approach it has established, where most of the common elements are shared between different unit designs, but some key specialized fixtures can still be adjusted directly. This means reducing the price customers have to pay, as there is no need to provide a completely new mold for each module, and the acquisition of additional capital equipment can be minimized. The new production line no longer needs to start from scratch, as only the earlier modules can be modified.
Harmonize the manufacturing technologies used, that is, meet the module requirements of more automotive customers through a highly adaptable platform. Customers can adopt unique units for their models, reducing total costs while maintaining their own profits, and this balance is very attractive to them.
Conclusion
It is clear that modern car manufacturers and their Tier 1 partners need superior interconnect devices. These products must not only provide the higher performance and long-term reliability that the field has always expected, but they must also go beyond the present to provide simple assembly and adequate adaptive range, thereby reducing total cost and maximizing yield.
The Interplex technology team has been serving customers in the automotive sector for decades, providing insight into the needs of new models currently in development, as well as vehicles that have yet to be released and are still in the concept stage. The addition of crimp terminals to the electronic control unit and sensor modules makes assembly easier, speeding up the production process to help increase profitability. In addition, by adopting a top-loaded, platform-based approach when building these modules, enough flexibility can be achieved to make the production process as cost-effective as possible.
The Products You May Be Interested In
![]() |
AMI-27B-12-3 | LINE FILTER 250VAC 12A CHASS MNT | 5796 More on Order |
![]() |
AMI-27A-12-3 | LINE FILTER 250VAC 12A CHASS MNT | 7380 More on Order |
![]() |
AMI-29-10-3 | LINE FILTER 110/250VAC 10A CHAS | 5292 More on Order |
![]() |
AMI-23B-20-6 | LINE FILTER 250VAC 20A CHASS MNT | 7200 More on Order |
![]() |
AMI-22A-20-6 | LINE FILTER 250VAC 20A CHASS MNT | 6804 More on Order |
![]() |
AMI-26B-10-3 | LINE FILTER 250VAC 10A CHASS MNT | 8226 More on Order |
![]() |
AMI-M12L-1-20-C | LINE FILTER 250VAC 1A CHASS MNT | 6534 More on Order |
![]() |
AMI-22A-16-3 | LINE FILTER 250VAC 16A CHASS MNT | 7164 More on Order |
![]() |
AMI-M11H-1-6-A | LINE FILTER 250VAC 6A CHASS MNT | 6120 More on Order |
![]() |
AMI-22A-12-1 | LINE FILTER 250VAC 12A CHASS MNT | 6678 More on Order |
![]() |
AMI-21-13-3 | LINE FILTER 250VAC 13A CHASS MNT | 7056 More on Order |
![]() |
AMI-21A-12-3 | LINE FILTER 250VAC 12A CHASS MNT | 5634 More on Order |
![]() |
AMI-M12B-1-3-B | LINE FILTER 250VAC 3A CHASS MNT | 5490 More on Order |
![]() |
AMI-M31NA-6A-50-D | LINE FILTER 50A CHASSIS MOUNT | 6624 More on Order |
![]() |
AMI-27B-10-1 | LINE FILTER 110/250VAC 10A CHASS | 6660 More on Order |
![]() |
AMI-M11Q-6-30-C | LINE FILTER 250VAC 30A CHASS MNT | 7092 More on Order |
![]() |
AMI-M11P-6-20-C | LINE FILTER 250VAC 20A CHASS MNT | 7596 More on Order |
![]() |
AMI-22-20-6 | LINE FILTER 250VAC 20A CHASS MNT | 5202 More on Order |
![]() |
AMI-23B-16-1 | LINE FILTER 250VAC 16A CHASS MNT | 6696 More on Order |
![]() |
AMI-M11P-3-6-B-1 | LINE FILTER 250VAC 6A CHASS MNT | 3798 More on Order |
![]() |
AMI-29-1-1 | LINE FILTER 110/250VAC 1A CHAS | 5796 More on Order |
![]() |
AMI-22-10-1 | LINE FILTER 250VAC 10A CHASS MNT | 5832 More on Order |
![]() |
AMI-M11J-3-2-B-1 | LINE FILTER 250VAC 2A CHASS MNT | 6102 More on Order |
![]() |
AMI-M11A-1-10-B | LINE FILTER 250VAC 10A CHASS MNT | 4266 More on Order |