How to optimize the wafer slicing process to improve chip yield
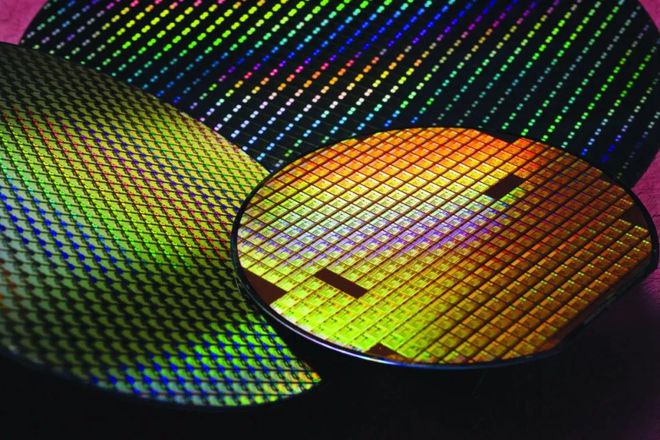
In semiconductor manufacturing, the wafer slicing process can be too important, it not only has a direct impact on the quality of the following chip, but also relates to the efficiency and cost of the overall production. In order to do the best wafer slicing process, so that the chip yield is raised, manufacturers have to consider from many aspects, such as materials, equipment, process parameters and so on, these factors have to be integrated.
Let's start with the selection of wafer materials. What material is used to make the wafer, which has an impact on the slicing process can not be underestimated. Commonly used wafer materials are silicon, gallium arsenide, gallium nitride these. The mechanical properties and electrical conductivity of different materials are not the same, and the right choice of the appropriate wafer material can not only make the cutting speed faster, but also reduce the chip problems in the cutting process.
Just like using a high-purity monocrystalline silicon wafer, you can significantly reduce the problems in the crystal, so that the product quality is better in the following process steps. And when choosing materials, you also have to consider the thickness and diameter of the wafer. Wafer thinner, although it can save some material, it can be easily deformed when cutting, so the selection of materials must be considered according to the specific place where it is used and the packing density of materials.
Let's talk about upgrading the slicing equipment. The performance of slicing equipment directly determines the accuracy and speed of cutting. With the continuous development of science and technology, water knife cutting, laser cutting, diamond wire cutting these new technologies are slowly used in the process of wafer slicing.
Water knife cutting technology relies on high pressure water flow with abrasive to cut, cut out the edge is particularly neat, the heat affected area is also small. Laser cutting is fast and accurate, but it may cause small cracks in the wafer due to thermal effects. Therefore, the reasonable selection of slicing equipment, but also the equipment configuration optimization, which can be too important. In addition, it is necessary to regularly maintain the equipment, to ensure the stable operation of the equipment, and avoid problems with the slicing process because of the failure of the equipment.
Then the precise control of cutting parameters. Cutting parameters are cutting speed, feed rate and cutting depth, and adjusting these parameters has a significant impact on the quality of wafer slices. Manufacturers can find the most suitable cutting parameters by doing experiments and analyzing data. For example, if the cutting speed is lowered properly, the heat can be reduced to concentrate together, so that the thermal stress on the wafer surface is small, and the chance of damage is low.
In addition, the feed rate is adjusted well, and the mechanical impact on the wafer can be reduced while cutting, which can help to improve the yield. At the time of cutting, staring at these parameters in real time, and keeping the process in the best state through feedback adjustment, the yield of the EVM1DSW30B25 chip can be greatly improved.
Wafer positioning and support are also particularly critical in the slicing process. If the positioning is not accurate and the support is not uniform, there will be stress concentration when cutting, which is easy to crack or defect the wafer. Therefore, it is necessary to use high-precision positioning machinery to optimize the support structure, so that the cutting precision and yield can be effectively improved.
Today's slicing equipment generally uses vacuum clamping technology, so that the wafer is stable when cutting. In addition, the reasonable design of the support structure, as far as possible to make the support area small, so that you can reduce the interference on the cutting edge, these are important ways to improve the quality of cutting.
Wafers that have usually been sliced have to undergo post-processing, such as removing burrs, cleaning, and surface treatment. These post-treatment processes can remove residual impurities from the cutting process, so as not to affect the subsequent packaging or testing. According to the standard post-processing process to do, and then use automated equipment, you can improve the efficiency and quality of processing, and further raise the yield.
For example, when deburring, you can use milling and polishing to ensure that the edge of the wafer is smooth, so that the generation of micro-cracks can be reduced. The cleaning process behind it, use ultrasonic cleaning machine, and then with chemical cleaning agent, so that the decontamination effect is the best.
The Products You May Be Interested In
![]() |
AOZ8530DI | FILTER LC(PI) 17NH/16PF ESD SMD | 6138 More on Order |
![]() |
AOZ6232QI#A | IC USB 2.0 SWITCH 10QFN | 3924 More on Order |
![]() |
AOZ1072AI_5#A | IC REG BUCK ADJ SYNC 8SOIC | 4320 More on Order |
![]() |
AOZ1073AIL_3 | IC REG BUCK ADJUSTABLE 3A 8SO | 7560 More on Order |
![]() |
AOZ1017AI | IC REG BUCK ADJUSTABLE 3A 8SO | 3330 More on Order |
![]() |
AOZ1321DI-04 | IC LOAD SW HI SIDE P-CH 4DFN | 6138 More on Order |
![]() |
AO4914L | MOSFET 2N-CH 30V 8A | 5130 More on Order |
![]() |
AO6804A | MOSFET 2N-CH 20V 5A 6TSOP | 5868 More on Order |
![]() |
AOT10B60D | IGBT 600V 20A 163W TO220 | 7740 More on Order |
![]() |
AO4447AL | MOSFET P-CH 30V 8SOIC | 2160 More on Order |
![]() |
AO4454L | MOSFET N-CH 100V 8SOIC | 8460 More on Order |
![]() |
AON7440 | MOSFET N-CH | 3006 More on Order |
![]() |
AOB210L | MOSFET N-CH 30V 20A TO263 | 3402 More on Order |
![]() |
AOW292 | MOSFET NCH 100V 105A TO262 | 2466 More on Order |
![]() |
AOW284 | MOSFET N-CH 80V 15A TO262 | 4374 More on Order |
![]() |
AOT11S65L | MOSFET N-CH 650V 11A TO220 | 7938 More on Order |
![]() |
AON6560 | MOSFET N-CH | 2232 More on Order |
![]() |
AOT430 | MOSFET N-CH 75V 80A TO-220 | 7326 More on Order |
![]() |
AOT8N65 | MOSFET N-CH 650V 8A TO220 | 6102 More on Order |
![]() |
AON2240 | MOSFET N-CH 40V 8A 6DFN | 2484 More on Order |
![]() |
AOTF296L | MOSFET N-CH 100V 10A TO220F | 15096 More on Order |
![]() |
AON6796 | MOSFET N-CH 30V 32A DFN | 7560 More on Order |
![]() |
AOT414 | MOSFET N-CH 100V 43A TO-220 | 17322 More on Order |
![]() |
AOZ8906CI | TVS DIODE 5.5V 8V SOT23-6 | 2664 More on Order |