From materials to processes, unlock the secrets of pressure sensor films
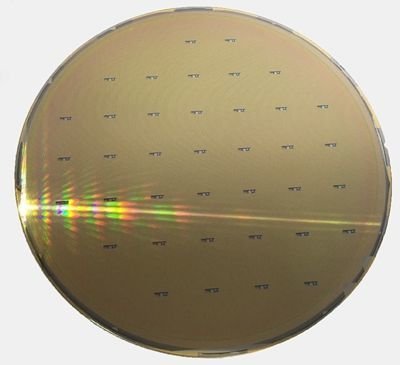
In today's modern science and technology field, pressure sensors are widely used, whether it is automobiles, aviation, medical, consumer electronics and many other fields, you can see it. Here, thin film pressure sensors are particularly popular. Why? Because of its small size, high sensitivity, anti-interference ability is also quite strong. Let's take a good look at the material, design and manufacturing process of this thin film pressure sensor, and figure out those technical doors behind it.
一.The working principle of the thin film pressure sensor
Thin film pressure sensors work by measuring pressure through piezoelectric effects or changes in resistance. What does that mean? That is, when there is pressure outside the sensor on the surface of the film, the film will be slightly deformed, and in this change, the resistance or voltage inside it will change. Then there is a measuring circuit inside the sensor that converts these changes into an electrical signal that can be read, so that the pressure can be accurately measured.
二.The choice of materials
The performance of the thin film pressure sensor is greatly related to the material selected. Common materials used are metals, semiconductors, and polymers. Let's start with metal materials, such as aluminum, nickel, copper, metal materials have good electrical conductivity and high mechanical strength, so they are used quite a lot. Semiconductor materials, such as silicon, have very special electrical properties and can be adjusted, and many sensors with high sensitivity requirements love to use it. Then there is the polymer material, which is flexible, and compared with metal materials, it is more suitable in some special occasions, and now it is more and more common in flexible sensor components.
1. Metal material: a Metal film is generally made on the substrate using physical vapor deposition (PVD) technology to make a film. It conducts electricity well and can ensure that the sensor is stable under high frequency signals.
2. Semiconductor materials: Semiconductor films are generally prepared by chemical vapor deposition (CVD) or ion implantation technology. Silicon is an interesting material. Its resistance changes linearly with pressure, so it is often the core material in thin-film pressure sensors.
3. Polymer materials: like polyimide (PI) and polyester film, these polymer films are lightweight, flexible, and chemically stable, which is quite ideal for flexible sensors. These materials are usually applied to the substrate by a coating or spraying process.
三.Production process
The manufacturing process for thin film pressure sensors can be complex, with many steps such as film deposition, pattern processing, and packaging.
1. Film deposition: According to the selected material, choose the appropriate deposition method. For metal materials, commonly used physical vapor deposition techniques such as evaporation and sputtering come in handy, semiconductor materials, usually using chemical vapor deposition. These deposition processes can be carried out in a tightly controlled environment to ensure that the resulting film is uniform and dense.
2. Pattern processing: After the film is deposited, it must be processed into a specific pattern by a photolithography or etching process. Photolithography is the use of photosensitive materials under ultraviolet light to biochemical changes, so that patterns can be transferred. The etching process removes areas of the film that are not protected by the photoresist in order to expose the underlying material, which is important for precisely controlling the sensitivity and response characteristics of the sensor.
3. Packaging technology: In order to prevent the film sensor from being affected by the external environment, packaging technology can not be less. Good packaging can not only block moisture and dust, but also provide the necessary mechanical support for the sensor. Common packaging materials are plastic, glass and ceramic, which must be considered when choosing a sensor working environment that does not match.
4.Testing and calibration: After the sensor is manufactured, it is also important to test and calibrate its performance. Add a known pressure signal to it, write down the sensor output electrical signal, and then compare with the theoretical value to ensure that the linearity and repeatability of the EVM1XSX50B15 (100KΩ) sensor is good. This process is generally carried out in a standard test environment, which can eliminate external factors such as temperature and humidity.
四,The application of thin film pressure sensor
Thin-film pressure sensors have excellent technology and excellent performance, and are widely used in many fields. In the automotive industry, it can be used to measure the pressure inside the engine cylinders, which can make combustion more efficient. In the aerospace sector, it can monitor air pressure changes in aircraft to ensure flight safety. In medical devices, it can accurately measure various physiological parameters in the patient's body, such as blood pressure, respiratory pressure, etc., which can help doctors make medical decisions in time. In addition, in the field of consumer electronics, it can also achieve touch sensing, so that the user experience is better.
五.Future development
With the continuous progress of technology, thin film pressure sensors will develop in the direction of higher integration, stronger intelligence and wider applicability. The development of new materials and the use of nanotechnology could lead to sensors with higher sensitivity and lower power consumption. Combined with artificial intelligence and Internet of Things technology, future pressure sensors can not only accurately measure data, but also analyze and feedback in real time, providing important support for smart cities and smart manufacturing.
The film pressure sensor has been comprehensively analyzed from the material to the process, and the science and technology door here is fascinating, and has laid a very solid foundation for our life and scientific and technological progress.
The Products You May Be Interested In
![]() |
TPCM-2.4-5 | CMC 2.41MH 5A 2LN TH | 6894 More on Order |
![]() |
62045-P2S02 | XFRMR TOROIDAL 10VA CHAS MOUNT | 2430 More on Order |
![]() |
62044-P2S02 | XFRMR TOROIDAL 10VA CHAS MOUNT | 6048 More on Order |
![]() |
62043-P2S02 | XFRMR TOROIDAL 10VA CHAS MOUNT | 5472 More on Order |
![]() |
62035-P2S02 | XFRMR TOROIDAL 7VA CHAS MOUNT | 6642 More on Order |
![]() |
62034-P2S02 | XFRMR TOROIDAL 7VA CHAS MOUNT | 7938 More on Order |
![]() |
62012-P2S02 | XFRMR TOROIDAL 3.2VA CHAS MOUNT | 3204 More on Order |
![]() |
62073-P2S02 | XFRMR TOROIDAL 35VA CHAS MOUNT | 5292 More on Order |
![]() |
70074K | XFRMR TOROIDAL 35VA THRU HOLE | 6840 More on Order |
![]() |
70072K | XFRMR TOROIDAL 35VA THRU HOLE | 5634 More on Order |
![]() |
70054K | XFRMR TOROIDAL 15VA THRU HOLE | 4716 More on Order |
![]() |
70041K | XFRMR TOROIDAL 10VA THRU HOLE | 2826 More on Order |
![]() |
70031K | XFRMR TOROIDAL 7VA THRU HOLE | 8658 More on Order |
![]() |
70015K | XFRMR TOROIDAL 3.2VA THRU HOLE | 7578 More on Order |
![]() |
70013K | XFRMR TOROIDAL 3.2VA THRU HOLE | 4392 More on Order |
![]() |
70003K | XFRMR TOROIDAL 1.6VA THRU HOLE | 2520 More on Order |
![]() |
70002K | XFRMR TOROIDAL 1.6VA THRU HOLE | 5040 More on Order |
![]() |
70025K | XFRMR TOROIDAL 5VA THRU HOLE | 4068 More on Order |
![]() |
62082-P2S02 | XFRMR TOROIDAL 50VA CHAS MOUNT | 4986 More on Order |
![]() |
62060-P2S02 | XFRMR TOROIDAL 25VA CHAS MOUNT | 23778 More on Order |
![]() |
70064K | XFRMR TOROIDAL 25VA THRU HOLE | 13758 More on Order |
![]() |
70034K | XFRMR TOROIDAL 7VA THRU HOLE | 8088 More on Order |
![]() |
AC1050 | CURR SENSE XFMR 50A T/H | 7362 More on Order |
![]() |
AC1010 | CURR SENSE XFMR 10A T/H | 5963 More on Order |