From 2D to 3D: How is Hybrid bonding changing chip design
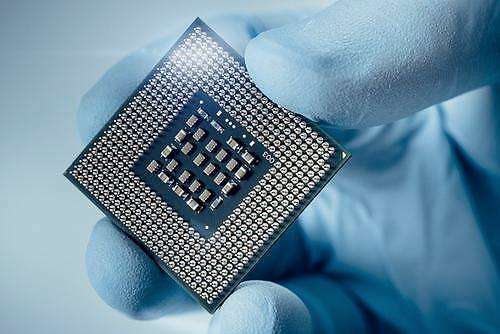
Chip design has undergone a major revolution. In the past, the traditional 2D chip design, although it has contributed a lot to the success of electronic products, and now the application needs are becoming more and more complex, it is a little confused and a little powerless. As a result, the idea of 3D chip design has slowly become mainstream, especially the Hybrid Bonding technology, which brings new hope and big breakthroughs in chip design.
What is hybrid bonding?
Hybrid bonding is a new packaging technology that can connect different materials together with special precision and strength. Specifically, it integrates chemical and physical bonds, using very small layers of metal and insulation, so that different types of chips, such as logic chips and memory chips, can be tightly integrated on a single platform. Compared with the old welding and plugging technology, hybrid bonding can significantly reduce the distance between chips, so that electrical performance and heat dissipation efficiency are greatly improved!
What are the benefits of 3D chip design?
First, it can reduce the size. By stacking multilayer circuits vertically, more functions can be integrated in the same size area. This means that designers can put more powerful processing capabilities in a smaller place, providing more flexibility and innovation possibilities for mobile devices, wearables, and iot devices.
Second, performance can also be improved. Hybrid bonding technology can not only effectively reduce the distance between the chips, but also greatly improve the communication speed. Because the distance of the signal transmission is shorter, the delay of the wire is less, and the electrical performance will naturally go up. This is very important in the context of high-speed computing and dealing with big data.
In addition, energy consumption can be optimized. As design changes, power management becomes important. Because hybrid bonding reduces the potential resistance between chips, the chips require significantly less energy to operate. On the one hand, this has a good impact on the battery life of mobile devices, and on the other hand, it is also in line with the environmental trend of modern electronic devices.
Finally, it can be integrated with multiple functions. Hybrid bonding can integrate chips with different functions on a single platform, such as logic and storage modules, which can not only improve the efficiency of the system, but also create some new design ideas. Designers can flexibly combine modules with different functions according to needs to better meet the needs of the market.
In practical applications, hybrid bonding technology can be used everywhere, from smartphones to data center servers. For example, some high-end smartphones have begun to integrate 3D camera heads and processing modules together, which can make the camera system more advanced. In the data center, the 3D stacked storage method can increase the storage density and access speed, so the overall computing performance is also up.
In the field of artificial intelligence (AI) and machine learning, hybrid bonding technology also shows great potential. Large models have to process a lot of data and calculations, which requires the chip to perform complex calculations and data transmission quickly and with less energy consumption. With hybrid bonding, AI hardware can do more work in less time, pushing intelligent applications forward.
Although there are many benefits of hybrid bonding technology, there are many difficulties in promoting it. First, the manufacturing process is too complex, and the production cost will go up, which will affect the market to a certain extent. Secondly, the issue of material selection and process compatibility must also be considered. Designers have to find the most suitable connection points between different materials in order to ensure the performance and reliability of the final product.
In addition, the problem of thermal management comes with it. In the 2D design, the heat management is relatively simple, but to the 3D design chip stack up, the heat is concentrated, which requires the designer to take into account the Monte Carlo method and thermal dispersion structure at the beginning of the design, to ensure that the product can be stable under various working conditions.
Look to the future
In the future, hybrid bonding technology will certainly continue to develop and become better and better, pushing chip design to a higher place. With advances in materials science and nanotechnology, the efficiency and reliability of hybrid bonding will continue to improve. At the same time, 3D chip design can make integrated circuit (IC) design more dense and complex, so that it can meet the needs of a variety of industries, from automotive to medical equipment.
Sharing and cooperation will be important factors in making this technology develop. With the establishment of the design specification bit by bit, the cooperation of enterprises up and down the industrial chain will become a common thing. This will not only reduce costs, but also allow hybrid bonding technology to get to market faster. Designers, engineers, and materials scientists work together to set standards that will ensure that new technologies continue to innovate and be used more and more widely.
By combining with emerging technologies such as 5G, Internet, and artificial intelligence, hybrid bonding energy promotes innovation in chip design to meet the needs of future society for high-performance, efficient, and diversified electronic products. In the face of the challenges of the future, designers not only have to consider whether the design is good-looking and practical, but also have to carry out more detailed technical innovation in a particularly small place to achieve a more perfect scientific and technological dream.
The Products You May Be Interested In
![]() |
CCR0512FPSXXZ01A | AC/DC CONVERTER 12V 500W | 5040 More on Order |
![]() |
150034920 | AC/DC CONVERTER 12V 750W | 5382 More on Order |
![]() |
PNDT003A0X43-SRZ | MODULE DC DC CONVERTER | 8352 More on Order |
![]() |
150043980 | DC DC CONVERTER 0-1.5V | 5328 More on Order |
![]() |
EHHD010A0B41-SZ | DC DC CONVERTER 12V 120W | 5112 More on Order |
![]() |
EQW030A0F41Z | DC DC CONVERTER 3.3V 99W | 4464 More on Order |
![]() |
AXH010A0M9-SRZ | DC DC CONVERTER 1.5V 15W | 4860 More on Order |
![]() |
QRW035A0F1Z | DC DC CONVERTER 3.3V 116W | 6894 More on Order |
![]() |
QW050F1 | DC DC CONVERTER 3.3V 33W | 5688 More on Order |
![]() |
QRW035A0G41 | DC DC CONVERTER 2.5V 88W | 6606 More on Order |
![]() |
QBW018A0B71-H | DC DC CONVERTER 12V 216W | 6786 More on Order |
![]() |
NH020Y2 | DC DC CONVERTER 1.8V 20W | 6372 More on Order |
![]() |
JC075B1 | DC DC CONVERTER 12V 75W | 6408 More on Order |
![]() |
HW004A0A-S | DC DC CONVERTER 5V 20W | 4716 More on Order |
![]() |
ATH006A0X4-SR | DC DC CONVERTER 0.8-3.6V 21W | 8064 More on Order |
![]() |
AXH005A0X-SR | DC DC CONVERTER 0.8-3.6V 18W | 5106 More on Order |
![]() |
JRCW016A0R641Z | DC DC CONVERTER 28V | 8766 More on Order |
![]() |
JRCW450R41-18Z | DC DC CONVERTER 32V 450W | 5310 More on Order |
![]() |
PIM400K8Z | DC DC CONVERTER -48V 400W | 7308 More on Order |
![]() |
NSR060A0X43Z | DC DC CONVERTER 0.6-5V 300W | 8154 More on Order |
![]() |
APXS006A0X4-SRZ | DC DC CONVERTER 0.6-5.5V 32W | 7200 More on Order |
![]() |
SSTW005A0F41Z | DC DC CONVERTER 3.3V 17W | 7326 More on Order |
![]() |
SHHD005A0F41Z | DC DC CONVERTER 3.3V 15W | 21864 More on Order |
![]() |
ATH010A0X3-SRZ | DC DC CONVERTER 0.8-3.6V 36W | 15948 More on Order |